How Indonesia Furniture Manufacturers can Save You Time, Stress, and Money.
How Indonesia Furniture Manufacturers can Save You Time, Stress, and Money.
Blog Article
The Facts About Indonesia Furniture Manufacturers Revealed
Table of ContentsThe Ultimate Guide To Indonesia Furniture ManufacturersSome Known Details About Indonesia Furniture Manufacturers Top Guidelines Of Indonesia Furniture ManufacturersMore About Indonesia Furniture ManufacturersIndonesia Furniture Manufacturers for DummiesThe Main Principles Of Indonesia Furniture Manufacturers
During a 30 year period, consisting of routine upgrades of wheels, control systems, fabrics, and various other elements, the prospective product savings from keeping such a chair in use, compared to the manufacture, usage and disposal of three 'standard' workdesk chairs, can complete more than 4.000 tonnes. In terms of business advantages, FAAS means Ahrend can have a closer partnership with clients and there is potential for better earnings.
If they have actually left over furniture in one facility, Ahrend can match it with need in another center (Indonesia furniture manufacturers). Generally, the FAAS version provides customers more adaptability around intending cycles which are typically 5-8 years (for example, due to changing work force and new ways of working), while furniture quickly lasts much longer
All of this suggests that circular economy thinking is the bright choice for a workplace furniture sector that can operate in the long term.
In the dynamic landscape of furnishings production, remaining in advance of the curve is paramount. Let's dive right into the game-changing advantages that digital warranty management brings to furniture suppliers.
The Facts About Indonesia Furniture Manufacturers Revealed
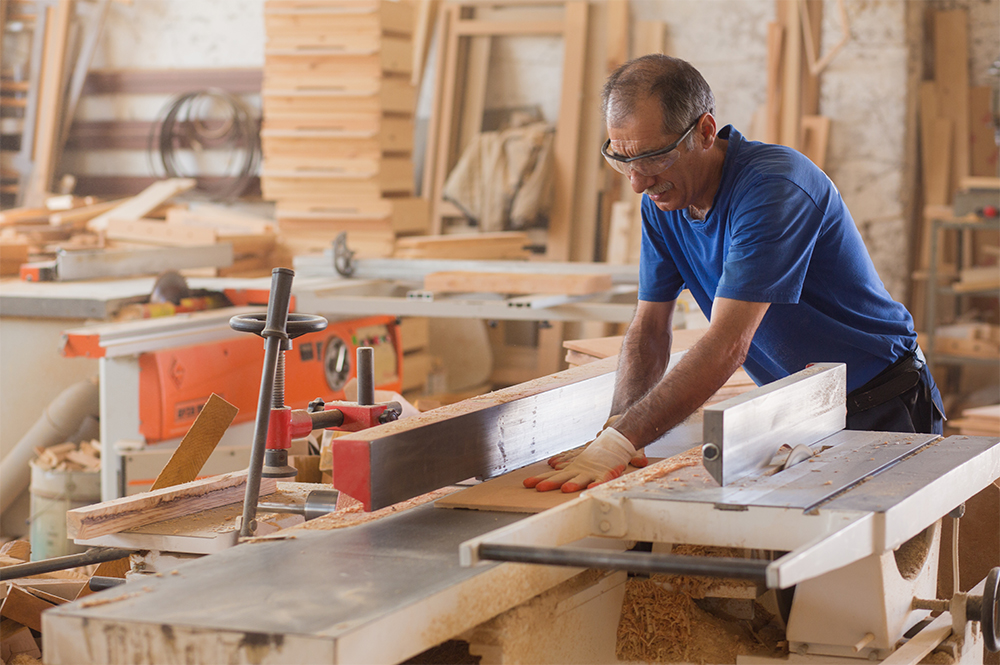
By only generating after the client has actually put the order, they will certainly create the, which helps in reducing inventory levels, prices and in turn, waste. Transferring to a demand-based production likewise implies created by 'quick furnishings' and press manufacturing in general. According to the U.S. Epa (EPA), greater than 12 million bunches of furniture waste are given garbage dumps annually.
It likewise stays clear of the mistake of the "fast furniture" frame of mind, which sees furnishings as a disposable great to be replaced as fads alter. On-demand manufacturing is for furnishings companies, as they are creating exactly what their customers desire (no projections needed), in regards to quantity and quality. This suggests smaller sized stocks and less markdowns.
See This Report on Indonesia Furniture Manufacturers
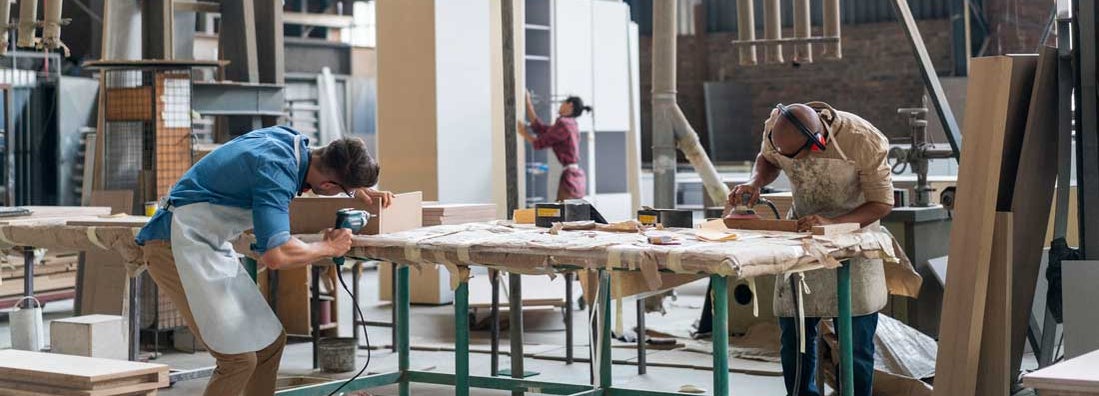
Prior to utilizing Furnishings As needed, operators reduced items which were after that placed in a large pile and relocated to the sewing space when they had time. Now, they have the ability to reduce only what is needed for the following day's stitching operations. Ekornes, a Lectra consumer for over 20 years, had actually used a batch manufacturing design for many years but they desired to trying out a brand-new manufacturing approach.
An experiment with one-piece flow produced substantial, favorable outcomes. Manufacturing lead-time was halved and final assembly lead-time was reduced by 94%. There was also a reduction in barrier supply from 1.5 days to 0.5 days in between sawing and last assembly. While thehas countless benefits for upholstered furnishings manufacturers, it does have its shortcomings too, one of which is.

The 6-Minute Rule for Indonesia Furniture Manufacturers
Having a product in 3D is the secret to an organization's success. Companies can come to be larger, much better, and more affordable with our aid. At CGIFurniture, we understand that one of the most crucial facets of a service is its product discussion. And the best way to sell a product is by see this website revealing it in its complete magnificence, which can be done successfully with 3D item visualization technology.
Product 3D visualization, also called 3D rendering or computer-aided design (CAD), is an extremely helpful collection of tools and remedies for marketing products online. It is also a new kind of aesthetic advertising that gives companies the ability to offer an interactive, photorealistic representation of items. Today, the majority of customer interactions happen online.
Every one of that will certainly enhance profit margins overall. The advantages of 3D product visualizations for furniture business provide you a lot more control over the product look when production. You can make changes to your layout as required, which will certainly save more time and money while doing so. When it comes to sales, absolutely nothing matters a lot more than the client's first impact.
Get This Report about Indonesia Furniture Manufacturers
This process calls for specialist CG musicians that have actually fully grasped their art. The turnaround time for 3D product visualization is extremely quick. When you have a brief and the pictures of your products, you can expect to obtain your initial draft within 1 day. The time it takes to consist of even more aspects like background, lighting, appearances, and decorations will certainly depend upon the number of modifications you need.
This method, website here furniture designers can select the ideal alternative and then relocate on to the next phase of development. You can utilize 3D modeling software program to develop digital prototypes of your items with actual measurements and functions.
It creates an impression initially look and makes it much easier for clients to figure out if they want to buy or not inevitably resulting in raised conversions. Give your customers a virtual preview inside of your item and reveal them just how to utilize it and its functions.
This is since a great deal of furnishings brands have actually not been making use of 3D item visualization which would certainly suggest that they can not use an experience just as good as yours. The 3D innovation makes it possible to use even more varied aesthetic options images, animations, 360-degree views, arrangements, and much more. view publisher site At the exact same time, all these take less time and initiative than ordinary photo fires.
3 Simple Techniques For Indonesia Furniture Manufacturers
Look into 3D rendering solutions for office furniture to raise your sales in no time. If you want this technology yet aren't sure where to begin, just contact us at CGIFurniture. We provide 3D providing services and solutions that are excellent for all kinds of furnishings shops, from local stores to large representatives.
Our members are committed to providing new employees a fulfilling and fascinating career course within the heart of British market, and to a much more sustainable future. Through The Future of Furnishings, our market discuss its operate in these two vital locations. On this page, tales from across our subscription, and from partners within our sector, will be frequently submitted.
Report this page